Designers may be surprised to learn what is possible when it comes to thermoforming large-sized heavy gauge parts such as mass transit interiors or full body MRI machines. At Kenson Plastics, we often have to educate our customers about the benefits of thermoforming and demonstrate to them when it would make sense as an alternative to injection molding (or other forming processes). Large-sized heavy gauge parts include kiosks, ATMs, large medical machines, and electronic housings for servers, among others.
Industrial Design Considerations for Large-Sized Heavy Gauge Thermoforming
Large-sized heavy gauge thermoformed parts make economic sense when you are dealing with lower volumes, which is often the case if you’re working with larger products. While vacuum forming and pressure forming processes are available, there are some considerations to keep in mind when designing large parts like kiosks, enclosures, or even server housings. In this blog, we’ll cover four of the main considerations that industrial designers should understand for large part heavy gauge thermoforming.

Being Strategic with Your Part / Mold Design
With larger parts being produced at low volumes you often see the realized result lacking the fit and finish of higher volume processes like injection molding. The suboptimal result is often a missed opportunity for the part designer and the production partner to collaborate on how to achieve the optimum results. If the designer and the engineering team collaborate early enough in the process, much consideration can be made with respect to how to manage the fit of adjoining pieces and minimizing tolerance stack in the overall assembly. If the engineering team has some design flexibility it is often possible to build in seam alignment and part to part referencing in features of the molded part which becomes “free” rather than having to try to manage fit through secondary finishing or other processing like under-skin frame supports or integrated fastening. The tolerance stack has a major impact on both the functionality and aesthetics of the final product. If you’re producing small volumes of items that sell at a high price, you need to make sure it looks and functions consistent with your customer’s expectations. Designers need to be strategic with how the different parts will overlap with other pieces.
For large-sized thermoformed mold design, remember:
- Exterior skins needs to remain sleek to match the desired fit and finish
- The mold will control the gap between sections and the alignment of the parts (instead of machining)
- It’s possible to include frame-deriving fits by using flexible fastening features
Lead Times for the Tooling
Larger parts like MRI machines or kiosks require longer lead times to machine the tooling which means you’ll need to get your custom thermoforming manufacturer involved as early as possible during the design iterations. Mold designs are critical to the success of the project. Molds often include intricacies like temperature control, “in-tool” actuation, or custom finishing depending on the part’s complexity. Kenson Plastics will work with you as a thermoforming partner through different iterations to find an ideal tool design that ensures you optimize the tolerances, radii, material selection, and finishing of the product.
Economies of Scale
In competitive markets, cost-dynamics favor thermoforming large parts over most lower volume alternatives. Compared to smaller parts where injection molding may be the cheaper option, thermoforming large parts is often the best option for cost, function and finish. You should consider each part and where the biggest cost/benefit lies when choosing which forming process to use.
Dimensioning and Draw Ratios
Large-sized heavy-gauge thermoforming can support draw ratios of more than 3:1, but engineers will need to remember that thinning is part of the process. Designers will need to calculate the required dimensions and consider the draw ratios as they relate to the final tolerances and required wall thickness.
Benefits of Thermoforming Large-Sized Heavy Gauge Parts with Kenson
Kenson Plastics works with various customers to deliver precise mold designs for any large-sized heavy-gauge thermoformed part. Our clients are often amazed at what the capabilities of thermoforming are and how cost-effective it is for larger product designs. Remember that high-precision fits are very possible – and with the right tool designs, you can thermoform large-sized overlapping parts that minimize seam openings.
To discuss your large-sized heavy-gauge thermoforming designs with a team of experts, get in touch with Kenson Plastics today.
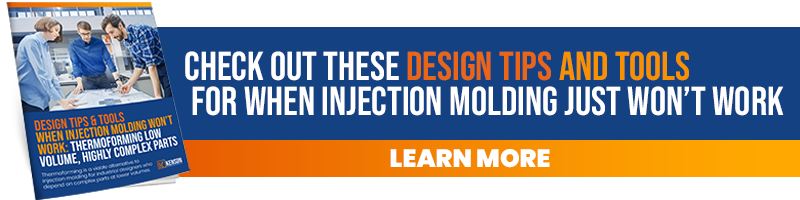