Getting from the drawing board to the first article inspection (FAI) in the shortest turnaround time isn’t a smooth, one-time-through process. Optimizing the design for manufacturing requires multiple iterations between product teams, potential suppliers, and manufacturing partners. One of the critical factors to consider when designing products and developing production techniques is part geometry. This will determine the cycle times during manufacturing and affect other factors like cost, quality, and appearance.
Assessing the part geometry in relation to the forming and assembly processes early in the design stages enables manufacturers to streamline the entire project’s lifecycle. The part geometry also affects the strength, durability, and overall performance of the final product. Considerations about the forming process, assembly method, and production lead time will determine what (if any) design changes you should make to the part’s geometry. If you want to arrive at a geometric design that optimizes all three of these areas, follow the tips below.
Tips for Optimizing Part Geometry for Improved Manufacturability
Part geometry is intrinsically linked to the product’s form, fit, and function (FFF). Whether you use this analysis to revise an existing bill of materials (BOM) or you are developing a new BOM for a prototype, it’s critical to remember that every design decision will not only affect the manufacturing cycles but also the appearance and features of the part.
The factors that may call for an updated design of the part’s geometry are:
- Molds and features - When the part has mounting locations, ribs, gussets, or other non-cosmetic functionality built into the geometry
- Finish and appearance - This could be a simple skin or cover that has the required texture, color, or cosmetic finish necessary for the desired aesthetics
The ideal design will incorporate both of these factors into the manufacturing and assembly operation. Taking this approach can drastically shorten the manufacturing lead time with secondary operations providing the required functionality and features without compromising aesthetics. The 3 tips below will help you dial in the design to achieve shorter lead times while maintaining the required quality and reducing costs with an optimized part geometry design.
Document the Functional Requirements of the Part
The part’s design intent will inform the functional requirements that are essential for it to work as designed. Documenting these requirements early in the project’s lifecycle will keep everyone involved on the same page, and allow you to identify where changes could improve the overall design.
Functional requirements translate into design features, which then become part of the part’s geometry. Feature specifications such as wall thickness, draft angles, and other structural elements like ribs, gussets, or threaded inserts can be derived from a well-documented functional requirement specification.
Iterate the Design with Expert Manufacturers
Molding and machining plastic parts have come a long way over the last decade. Advances in medical devices, transport interiors, and other sophisticated electronics paved the way for complex product designs to benefit from these manufacturing techniques.
When the functional requirements are in place, you can engage with an expert manufacturer that utilizes all of the latest production processes, including 3D scanning and modeling, thermoforming, CNC machining, and secondary operations such as bonding or painting. Any combination of these techniques can improve the final product design and optimize the geometry to meet the functional requirements.
Determine the Material Sourcing and Manufacturing Procedures
To reduce the manufacturing lead time, considerations about sourcing materials and streamlined manufacturing procedures should also factor into the part geometry. Material management and organization are critical elements that help ensure the success of a product.
Using a turnkey manufacturing partner like Kenson Plastics will give you access to the best suppliers and materials, ensuring your part complies with the exact specifications you need. From helping you dial in the part’s geometry and getting your design from the drawing board to FAI in the shortest lead times, we’ll also be able to advise on specific material characteristics, forming techniques, finishing procedures, and quality validation processes.
Shorten the Project Runway from Design to Delivery with Kenson Plastics
Kenson Plastics can assist with the shortest turnaround times when it comes to plastic part manufacturing. In most cases, we can get you from the design phase to first article inspection within 8-10 weeks. If parts are more complex and require more features, our experience can help you achieve a lead time that is still twice as quick as most of our competitors. Kenson Plastics can handle any of your unique part geometry requirements and ensure you have a shorter project runway to profitability.
To discuss your project with one of our team’s experts, contact us here.
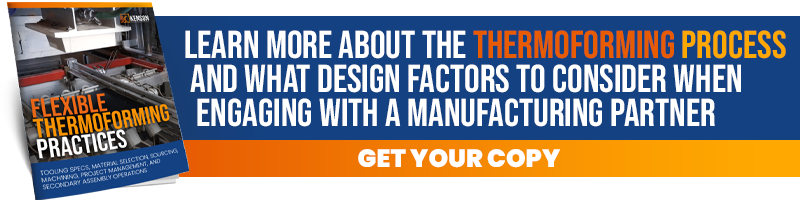