Improving lead times is how manufacturers maintain a competitive edge in today’s economic headwinds. Developing ways to shorten your lead times is a surefire strategy to increase profitability, improve customer satisfaction, and reduce costs.
In 2022, manufacturing lead times sapped the momentum out of a resurging US economy. Production delays also added additional price pressures to manufacturers, leading to increased inflation and falling demand. In this blog, we’ll look at some of the ways Kenson Plastics can help you improve lead times with thermoformed parts.
Factors that Affect the Lead Time of Thermoformed Parts
The total lead time of the project will include supply chain management, manufacturing time, and project management. Within each of these processes, Kenson Plastics work with our customers to find an optimized solution that streamlines the project runway.
Our approach uses design economy and ingenuity to achieve the shortest possible lead times without compromising product quality. Here are three ways to optimize your project execution with Kenson Plastics.
Engage Early to Iterate and Optimize the Design
The earlier you engage with us, the more value we can add to the project. If we’re involved during the prototyping stage, we can share our expertise about how to improve the design for manufacturability, provide advice on material selection, and help manage the project cost for low-volume, high-quality thermoformed parts.
The project elements where we can add value early include:
- Raw material selection and sourcing – Understanding the environment and application of the product allows us to recommend a suitable material that provides the required fit and finish.
- Part design validation – An extensive design review will determine the complexity of the part and enable us to optimize the specifications to reduce lead times and maintain the required tolerance stack.
Mold-making and secondary machining – We can help reduce the cycle time of a part by iterating the mold design and finding ways to minimize the complexity of secondary machining operations.
- Inspection and testing – To maintain the required quality, we will develop a robust testing and inspection regiment to validate the manufacturing process for repeatability (using 3D scanning technology to detect any interferences and fitment clashes).
Leverage our Purchasing Power
Supply chain issues remain one of the biggest factors when developing quality plastic parts. Mandatory minimum buys and raw material shortages can push a project’s schedule and drive up the price per part. Kenson Plastics works with customers in all industries, giving us an advantage when it comes to sourcing materials and limiting project costs.
Benefits of working with Kenson Plastics include:
- Extensive supplier network – We source from many different suppliers (and all our thermoplastics are made in the USA) to provide the shortest turnarounds when sourcing materials.
- Industry relationships – When schedules are tight, we can call in favors from our suppliers to streamline the project’s execution where other manufacturers aren’t able to succeed.
- Optimized manufacturing process – Because our customers produce parts for highly regulated industries such as aerospace and life sciences, we have a streamlined manufacturing process and a wide breadth of expertise that can adapt to almost any application.
Mitigate Product Liability Risks
Kenson Plastics can deliver production tooling and produce parts in as little as 6 to 8 weeks, depending on the overall design complexity. Using our experience, we can provide full turnkey projects where we remain accountable for all elements of the part’s quality. Our process is agile from the start to finish of the project, ensuring our customers benefit from shorter lead times and repeatable part manufacturing processes.
For turnkey projects, we will:
- Analyze the product’s design for manufacturability
- Source the materials required for tooling and manufacturing
- Develop the CNC program for secondary machining
- Add additional features with bonding or additive manufacturing
- Validate and inspect each part before secondary assembly
Reduce Project Runway and Optimize Manufacturing with Shorter Lead Times from Kenson Plastics
Kenson Plastics understands the urgency that comes with bringing complex products to market. Our team remains committed to working with customers that want to improve lead times and reduce project costs. As a complete turnkey manufacturing partner, Kenson Plastics has proven that our tool design and sourcing methods provide cost and quality benefits to our customers.
To get the process started today, reach out to Kenson Plastics and let’s talk about your project.
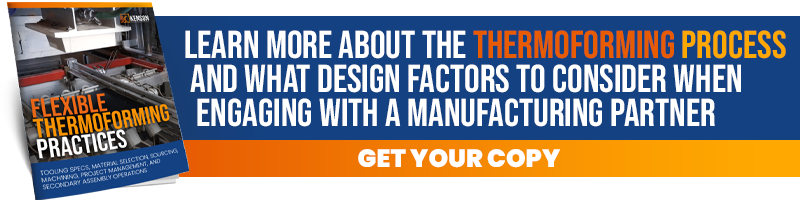